Deck Construction Costs Climb 23% in 2024 Breaking Down the Price Per Square Foot Across 7 Popular Materials
Deck Construction Costs Climb 23% in 2024 Breaking Down the Price Per Square Foot Across 7 Popular Materials - Rising Lumber Costs Push Cedar Deck Prices to $32 Per Square Foot
The cost of building a cedar deck has significantly increased, with estimates reaching $32 per square foot in 2024. This surge is primarily due to the ongoing increase in lumber prices. This price jump is part of a wider trend—the overall cost of deck construction is anticipated to rise by 23% in 2024. While past deck projects have seen a typical cost range of $20 to $40 per square foot, the escalating prices of natural wood materials, especially cedar, necessitate a reevaluation of project budgets. This upward trend impacts not only the material costs but also the labor associated with deck building, creating a challenging environment for homeowners. The combination of these factors means that building a new deck in 2024 might require more careful planning and potentially necessitate reconsidering deck materials or overall project scope, making the prospect of a new deck a more complex decision.
The escalating cost of cedar lumber, a consequence of ongoing supply chain difficulties and a surge in demand for outdoor spaces, has driven the price of cedar decks to an estimated $32 per square foot in 2024. This increase aligns with the broader trend of a 23% jump in overall deck construction costs this year. While cedar's inherent resistance to decay and its aesthetic appeal make it a desirable material, the heightened cost might give some homeowners pause.
The increased demand, likely fueled by a desire for outdoor living amid recent shifts in lifestyle and spending priorities, has impacted availability and influenced pricing. Furthermore, the majority of cedar used in US decks originates from the Pacific Northwest, making transportation costs and regional variations in supply play a major role in price differences across the country. The seasonality of lumber markets also contributes to fluctuating prices, with peaks often occurring in the spring and early summer as construction and DIY projects rise.
Despite the high price, cedar's natural properties like resinous oils and its durability, which can lead to a lifespan exceeding 25 years with proper upkeep, might still prove attractive to those seeking a long-lasting deck. However, cedar's natural characteristics also require attention to moisture content during storage, handling, and construction. Variations from optimal moisture ranges can contribute to warping and cracking. And while treatments to improve resistance and extend warranties can add value, they inevitably raise the overall cost. The interplay between these factors makes it interesting to observe how the rising cost of cedar might influence homeowners' choices between it and other decking materials, including composite or pressure-treated options. Especially when considering the DIY trend which is altering the market for both materials and installation labor. It remains to be seen if the premium price of a cedar deck can remain sustainable against these pressures over time.
Deck Construction Costs Climb 23% in 2024 Breaking Down the Price Per Square Foot Across 7 Popular Materials - Composite Decking Materials Hit $38 Per Square Foot Due to Supply Chain Issues

The cost of composite decking has skyrocketed, reaching an average of $38 per square foot. This substantial price increase is directly linked to ongoing supply chain problems that haven't shown any signs of easing. This surge in cost is part of a larger trend affecting the deck construction industry, with overall deck building costs anticipated to jump 23% in 2024. While composite decks are touted for their durability and ease of care, the prices can be a significant hurdle, with some top brands pushing the cost per square foot over $75. The combination of higher material costs and increased labor expenses makes building a deck in 2024 a more complex financial undertaking for many. Given the persistent supply chain issues, homeowners may find themselves reevaluating their deck material choices or perhaps reconsidering the scope of their projects in order to stay within budget.
The current average price of $38 per square foot for composite decking materials highlights the ongoing impact of supply chain issues. These difficulties, affecting the availability of raw materials like plastics and wood fibers, have pushed up manufacturing costs, making what was once perceived as a more budget-friendly option now a comparable financial hurdle to traditional materials.
The $38 price tag reflects not only the increased material costs but also the constraints of limited availability and inflated shipping expenses, consequences of both domestic and international supply chain bottlenecks. The complexities of sourcing and transporting these materials have become a critical factor in determining the final price.
Interestingly, composite decking, often containing up to 70% recycled content, appeals to homeowners seeking low-maintenance and durable options. However, the elevated price point raises questions about the true cost-effectiveness, especially as availability remains a challenge.
Current production capacity is struggling to keep pace with demand, resulting in manufacturing delays that further contribute to price increases. This inability to quickly respond to market demand raises concerns about the long-term stability of composite decking pricing.
The recent surge in popularity of outdoor living products, partly fueled by the growth of remote work, has significantly impacted demand for decking materials across the board. This increased demand has unfortunately driven prices artificially higher, showcasing how consumer trends can influence construction material costs.
Composite materials typically come with a 25-year or longer warranty, but the higher initial investment may not align with every homeowner's budget. This discrepancy necessitates careful consideration of long-term value versus immediate expenses when assessing the true worth of a deck built from these materials.
Composite decking manufacturing often involves processes that reduce the release of volatile organic compounds (VOCs) compared to treated wood. However, stricter environmental regulations, intended to support sustainable practices, ironically contribute to higher consumer costs. This challenges the notion that environmentally friendly materials should automatically translate into more affordable options.
While composite decks offer resistance to weathering, the associated installation costs can quickly escalate without proper planning. Finding qualified installers has become a major cost driver, adding another layer of financial complexity for homeowners considering composite materials.
The technical aspects of composite decking necessitate specialized tools and equipment for proper installation, which often adds to the overall labor cost compared to wood decks. This factor can make DIY projects less viable and further complicates budgeting for the entire project.
Given the ongoing supply chain issues, the price of composite decking materials is likely to remain unstable in the near future. Those contemplating a new deck should consider not just the current costs, but also the potential impact of future supply chain conditions on their investment over the long term.
Deck Construction Costs Climb 23% in 2024 Breaking Down the Price Per Square Foot Across 7 Popular Materials - Natural Hardwood Options Like Ipe Reach $45 Per Square Foot Mark
High-end natural hardwood options, like the popular Ipe, have become substantially more expensive in 2024. The cost for Ipe decking material alone is averaging $14 per square foot, though prices can vary from $10 to $25, which is a significant increase compared to previous years. If you factor in installation, the cost to build a deck with Ipe can easily reach $50 to $80 per square foot. A typical 200-square-foot Ipe deck might cost roughly $2,198 for the materials and shipping, but some retailers are pushing prices closer to $2,872, which emphasizes the potential for variation. Contributing to the price swings are factors like international shipping costs, the availability of imported Ipe, and the impact of new regulations taking effect in November 2024. While Ipe is prized for its durability and appearance, homeowners are likely to find similar price hikes with other hardwood decking materials, like Tigerwood, which is priced between $10 and $19 per square foot. With deck construction costs as a whole climbing 23% in 2024, it's become essential for homeowners to thoroughly assess different options and carefully consider the implications for both budget and desired aesthetics when deciding on a deck material.
While cedar and composite decking materials have seen significant price increases this year, pushing the cost per square foot to new heights, other natural hardwood options are also experiencing upward pressure. Specifically, Ipe, a dense and durable hardwood often referred to as Brazilian walnut, is now reaching the $45 per square foot mark for materials alone. This price increase, though substantial, is partially explained by the material's inherent properties and growing demand.
Ipe's remarkable density, with a specific gravity exceeding 1.0, means it's denser than water. This density translates into exceptional durability and resistance to insect damage, contributing to a lifespan that can reach 75 years with proper upkeep. It's also naturally resistant to decay, making it a popular choice for decks in humid or wet climates. Importantly, its inherent oil content helps keep the surface cooler than many other hardwoods or composite decking in direct sunlight, offering some respite during summer heat.
However, the cost of Ipe isn't solely driven by its physical attributes. A significant portion (around 20-30%) of the price comes from factors like international transportation and processing, primarily because much of it is imported from South America. This factor can introduce volatility in the market, with supply chain dynamics and global demand heavily impacting pricing. Interestingly, Ipe also boasts a variety of natural grain patterns, adding to its aesthetic appeal and contributing to the higher cost as some are willing to pay a premium for unique looks.
Compared to treated softwoods that often require yearly resealing, the maintenance of Ipe is more forgiving. Regular washing and occasional sanding and oil application are typically sufficient to maintain the material's rich color and visual quality over time. It naturally ages to a silver-gray, which is desirable by some, without compromising the structural integrity. This low-maintenance aspect, combined with its inherent durability, makes it a compelling choice for those seeking a low-effort, high-return deck material. Its strength also positions it well for commercial spaces, where high foot traffic and durability are prioritized.
The rise in price is likely also linked to an increased global demand for natural hardwood decking as more homeowners seek aesthetically pleasing, long-lasting solutions for outdoor living spaces. Yet, with the heightened demand comes challenges for local suppliers struggling to acquire enough Ipe, leading to price fluctuations in different regions. Homeowners considering Ipe need to be aware of this, as it's increasingly crucial to research local suppliers and evaluate the pricing landscape when budgeting for a decking project. The interplay of global demand, material characteristics, and the complexities of sourcing contribute to the higher prices and suggest that the trend of Ipe exceeding $45 per square foot might continue in the foreseeable future.
Deck Construction Costs Climb 23% in 2024 Breaking Down the Price Per Square Foot Across 7 Popular Materials - Pressure Treated Pine Remains Most Affordable at $15 Per Square Foot
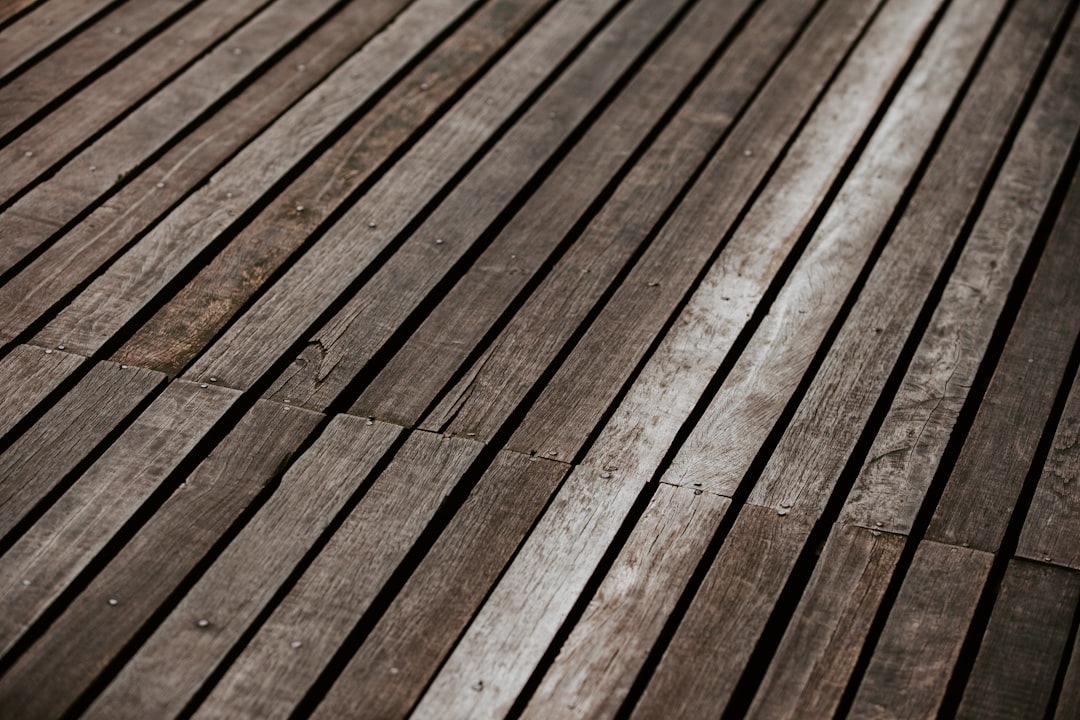
Even with deck construction costs generally rising 23% this year, pressure-treated pine remains the most budget-friendly decking material, holding steady at about $15 per square foot. This makes it an attractive choice for those looking to build a deck without breaking the bank. While a basic 100 square foot deck using pressure treated pine can cost between $1,500 and $2,500, significantly larger decks will naturally increase the total cost. This price point highlights the difference in cost when compared to more expensive materials like cedar or composite decking, which have seen much larger price increases. Pressure-treated pine, which can last between 10 and 25 years, offers a good balance of affordability and durability. With the cost of many other materials increasing, homeowners should carefully evaluate their priorities when selecting a decking material and think about the costs over the life of the deck, which includes both initial installation and ongoing maintenance.
Pressure-treated pine continues to be the most economical decking choice, coming in at roughly $15 per square foot. This makes it a considerably more budget-friendly option compared to materials like composite or hardwood decking, which can easily exceed $30 or even $40 per square foot.
The affordability stems from the chemical treatment process that pressure-treated pine undergoes. Preservatives are forced into the wood's structure, boosting its resistance to rot and insects and potentially extending its lifespan compared to untreated pine. This treatment is a key factor in its practicality, particularly when contrasted with the high initial investment of other options like composite decking.
Interestingly, despite its more economical nature, pressure-treated pine is quite versatile. Its ease of handling and shaping lends itself well to various design aesthetics, allowing for a wide range of custom looks without breaking the bank.
The chemical treatment also plays a role in enhancing moisture resistance. Chemicals like ACQ significantly reduce the risk of warping and splitting often seen in untreated softwoods, which can be a major factor in deck longevity. While it still requires some maintenance like periodic sealing or staining, the lifespan of a properly cared for pressure-treated pine deck can range from 15 to 20 years. This longevity, although shorter than some composite materials with longer warranties, provides a viable and more financially accessible alternative.
Moreover, pressure-treated pine is generally lighter than many hardwood materials, potentially simplifying handling and installation, especially for those tackling DIY projects. This could translate to lower labor costs, although labor costs in the overall deck construction industry are still expected to increase.
Unlike some composite or synthetic materials, pressure-treated pine is a natural product and therefore is generally easier to repurpose or recycle when it reaches the end of its useful life. While not a primary decision factor for many homeowners, it provides a potential advantage, depending on personal or environmental goals.
Furthermore, it retains the authentic look and feel of natural wood, offering a distinct aesthetic preference compared to the sometimes uniform appearance of composites. The ability to observe and interact with the natural wood grain and texture seems to attract certain individuals.
It is often easier to find readily available supplies of pressure-treated pine due to its widespread production across North America. This contrasts with imported hardwoods, which can experience more price volatility based on international shipping, supply chains, and regulations.
Despite needing appropriate storage and moisture control during the installation phase, pressure-treated pine proves more resilient to changes in temperature and humidity after being treated. This aspect contributes to a greater degree of environmental stability compared to untreated pine, mitigating potential challenges for the homeowner.
Overall, while pressure-treated pine is a solid, basic option that requires some care and maintenance, it offers the distinct advantage of affordability. The overall 23% industry cost increase seems less problematic when considering that treated pine is the least impacted option. That being said, homeowners must always carefully consider project scope, local labor rates, and material availability to ensure any budget remains realistic for the desired outcome.
Deck Construction Costs Climb 23% in 2024 Breaking Down the Price Per Square Foot Across 7 Popular Materials - PVC Decking Materials Surge to $41 Per Square Foot Following Factory Delays
PVC decking materials have become significantly more expensive, with the average cost now reaching $41 per square foot. Factory delays are a major factor driving up the price, adding to the overall 23% increase expected in deck construction costs throughout 2024. While PVC is often touted for its low-maintenance properties compared to wood, this cost surge raises questions about its value proposition. The current strong demand for outdoor living spaces makes choosing a deck material more complex, forcing homeowners to carefully weigh the cost against the desired qualities. The rising price of PVC highlights the broader challenges within the construction industry, making careful planning and evaluation even more important for those considering a new deck. It will be interesting to see how this impacts the long term popularity of PVC when compared to other options on the market.
The price of PVC decking has surged to an average of $41 per square foot in 2024, a significant increase compared to previous years. This jump can be attributed to a combination of factors beyond just factory delays, including a rise in demand for outdoor living spaces. This increased demand puts pressure on production, exacerbates existing supply chain disruptions, and further contributes to higher material costs.
PVC, being a durable plastic that resists moisture, is often chosen for its suitability in various weather conditions. However, it's important to acknowledge that PVC production is energy-intensive. This can influence the overall cost of the material and is something that researchers in the field are studying further.
One of the lesser-considered characteristics of PVC is its tendency to expand and contract with temperature shifts. This thermal expansion can be significant and requires careful attention during installation to prevent warping or buckling. This is something that impacts the installation process and adds a layer of complexity that needs careful consideration by installers and homeowners alike.
PVC decking often incorporates various additives to achieve the desired color and texture, enhancing its aesthetic appeal. But these additives also add steps to the manufacturing process. These steps also introduce quality assurance considerations that can further contribute to production bottlenecks and delays, ultimately impacting pricing.
When evaluating the cost-effectiveness of PVC versus traditional wood decks, it's worth noting that PVC generally boasts a longer lifespan, potentially reaching 25 to 40 years. While the initial investment is higher, the potential to reduce long-term maintenance costs might make it a compelling option for some.
This price increase, and the added cost compared to other options, has created a market trend where warranties play a larger role in homeowner choices. Manufacturers are responding by offering extensive warranties, sometimes extending up to 50 years, to highlight the potential long-term value of PVC despite its upfront costs.
Although marketed as low-maintenance, PVC may still require some specific cleaning products. These added costs should be factored into the overall budget alongside the initial purchase and installation.
The growing use of recycled content, with some PVC decking containing up to 25% recycled plastics, adds another dimension to the market dynamics. However, relying on recycled materials can create volatility in the supply chain, leading to price fluctuations and unpredictability.
While manufacturers are developing PVC that better mimics the aesthetic appeal of natural wood grain and texture, it is yet to be seen if this significantly alters the marketplace. Many consumers still find the organic look of traditional wood more desirable, potentially hindering the wider adoption of PVC, even with advancements in its aesthetic design.
As a consequence of the price changes, there is evidence of homeowners considering alternatives to PVC. These choices often include aluminum or different composite materials, reflecting both a desire to save costs and a broader trend in consumer tastes within the deck market. This evolving market creates interesting possibilities for research and could indicate longer-term shifts in deck material preference.
Deck Construction Costs Climb 23% in 2024 Breaking Down the Price Per Square Foot Across 7 Popular Materials - Aluminum Decking Costs Stabilize at $35 Per Square Foot Despite Metal Tariffs
Aluminum decking presents a relatively stable option in a market experiencing overall price increases. Despite metal tariffs that have impacted other industries, the cost of aluminum decking has settled around $35 per square foot. This price point keeps it competitive among other decking choices, although installation costs can vary significantly, ranging from about $23.50 to nearly $29 per square foot depending on the complexity of the project and the specific site. Homeowners are drawn to aluminum because of its inherent durability and the minimal upkeep it requires over time. This makes it a potentially attractive choice despite broader economic uncertainty.
Even though aluminum appears stable, the larger deck construction market is seeing a 23% overall price increase in 2024. This underscores the importance of carefully evaluating the many factors that can influence a deck project. For those seeking a durable, low-maintenance option that may be resistant to price fluctuations in the near future, aluminum might be a worthwhile consideration, although the long-term behavior of the market will depend on a variety of future conditions. Ultimately, homeowners must thoughtfully balance desired aesthetic qualities with the cost of materials and installation, especially when faced with broader price increases across the construction industry.
Aluminum decking presents an intriguing case study in the current deck construction landscape. While many materials have seen dramatic price increases in 2024, aluminum has remained relatively stable at around $35 per square foot. This stability, despite the imposition of metal tariffs, indicates a degree of market equilibrium that's worth examining.
The initial fear that tariffs would disrupt aluminum pricing hasn't materialized to the extent predicted. It seems that supply chains have adapted, or perhaps the demand for aluminum decking hasn't been as susceptible to price hikes as other materials like cedar or composite. This resilience could be related to the unique properties of aluminum that make it an attractive choice in certain situations.
Aluminum boasts a significant durability advantage, often lasting five decades or more with minimal upkeep. This long lifespan can ultimately make its initial cost more justifiable over time, compared to materials that might require more frequent maintenance or replacement. Its lightweight nature is also a benefit, especially when considering transport and installation, making it an attractive option for DIY projects. In contrast to many woods, it's naturally resistant to the elements like rust and corrosion, which can translate to fewer repairs and maintenance costs throughout its lifespan.
However, its thermal conductivity is a notable characteristic. Aluminum readily absorbs and transmits heat, which can lead to uncomfortable temperatures on the deck surface during sunny periods. Designers and installers need to account for this by incorporating elements like shading or perhaps careful material choices to address this.
The minimal maintenance requirements of aluminum are undeniable. Unlike traditional wood decks that demand regular staining or sealing, aluminum decks often only require occasional cleaning, which can be a major selling point for homeowners who prioritize low maintenance. The wide range of available finishes and colors also allows for a fair amount of flexibility in achieving desired aesthetic looks.
Interestingly, aluminum decking is often seamlessly integrated with other materials, such as composite or hardwood, in projects that require diverse aesthetics or functional elements. This versatility broadens its design applications, making it a more adaptable option compared to solely using a single material for an entire deck.
Aluminum's stability in a volatile market, coupled with its attractive durability and relatively low-maintenance profile, is fostering growth in its use. Urban environments, especially, are seeing a growing adoption of aluminum decking, likely due to its space-efficiency and long-term durability. This trend reflects a larger shift in homeowner priorities related to outdoor living as outdoor spaces are becoming increasingly important in a variety of settings. It will be interesting to see how aluminum's cost-effectiveness and its functional benefits play out in the market over time as competing material technologies and pricing structures evolve.
Deck Construction Costs Climb 23% in 2024 Breaking Down the Price Per Square Foot Across 7 Popular Materials - Modified Wood Products Average $28 Per Square Foot in Current Market
Modified wood products are currently priced at an average of $28 per square foot for deck construction. This falls within the broader context of deck building costs increasing by 23% in 2024. While modified wood offers a potentially attractive combination of durability and aesthetics, homeowners need to be aware of the financial implications of this price point. With the construction industry facing material price fluctuations and supply chain complexities, building a deck this year necessitates careful planning and budgeting, including a close examination of the costs and benefits of different decking materials. Considering the rising prices across the board, evaluating modified wood alongside other options becomes essential for ensuring a successful and affordable deck project.
Modified wood, a product of modern treatments aimed at enhancing wood's natural properties, currently averages around $28 per square foot. These treatments often focus on making wood more resistant to the damaging effects of moisture and insects, effectively extending the wood's lifespan. While this price might seem higher compared to untreated wood, the long-term cost-effectiveness can be better due to the reduction in maintenance requirements.
One advantage of modified wood is its superior decay resistance compared to traditional softwoods. Research indicates it significantly outperforms these options in environments prone to moisture, such as decks near pools or in humid climates. This heightened resistance translates into less frequent repairs or replacement over the wood's lifespan, potentially making it a cost-effective choice in the long run.
However, the installation process necessitates close attention to moisture content. If not handled correctly during storage and installation, modified wood can undergo dimensional changes that could impact its structural integrity and appearance. This requirement highlights a potential point of failure, and suggests that installers need to be well-versed in best practices when using modified wood.
The demand for modified wood products is growing, which is in line with the wider trend of consumers seeking more durable and longer-lasting materials for outdoor projects. It's interesting to consider that the desire for low-maintenance outdoor spaces is helping drive this market shift.
Though, it's important to note that price fluctuations can occur based on geographic location due to factors like production capabilities and shipping costs. Homeowners interested in using modified wood should research local suppliers to find the best price and options available in their area.
Further research into the thermal properties of modified wood has shown that it can have improved stability compared to traditional wood options, with less variation in expansion and contraction with temperature changes. This can be a factor that leads to less warping over time, which can be a benefit in environments with large shifts in daily and seasonal temperatures.
The growing popularity of DIY projects has led to an increased interest in modified wood. It seems to be a good fit for both novice and experienced DIYers due to its relative ease of workability and the reduced possibility of unexpected failures related to unpredictable moisture impacts.
Another advantage of modified wood is that it can often be integrated with other common decking materials. This creates flexibility in designing aesthetically pleasing decks while maintaining structural integrity.
The wood treatment and safety regulations are constantly evolving, and as these changes take effect, the modified wood industry is likely to adapt. These regulations might impact pricing or the specific characteristics of available products in the marketplace, so homeowners need to stay abreast of any such changes.
This overall picture of modified wood suggests that it might be a viable choice for those interested in a durable, longer-lasting decking option. However, homeowners should carefully consider the upfront cost relative to their needs and always factor in local material and labor costs when planning a project.
More Posts from cashcache.co: